Regardless of whether you’re a seasoned manufacturing veteran or just beginning to explore the realm of industrial production, understanding die-cutting and its benefits can revolutionize your operations. This article serves as a comprehensive guide to die cutting, highlighting the problems it addresses, its diverse applications, and why it’s considered an industrial game-changer. Dive in and discover how die-cutting could be the key to unlocking your business’s potential.
What is Die-Cutting?
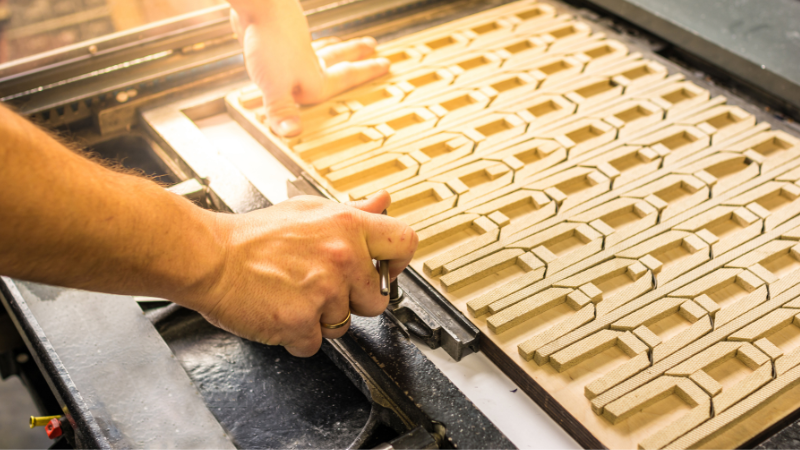
Many people haven’t heard about the benefits that die-cutting services provide, and that’s okay! In this section, we’re going to inform you about what exactly rotary die cutting is and how it can apply to your business work.
Understanding Die-Cutting
Die cutting is a fabrication process used to cut, shape, and form a wide range of materials using a die – a specialized tool similar to a cookie cutter. The die, crafted from sharp steel blades bent into the desired shape, is pressed onto the material (the workpiece) under high pressure to create precise cuts or impressions. This method is prized for its high-speed operation, consistency, and ability to produce complex shapes with impeccable precision.
Applications of Die-Cutting
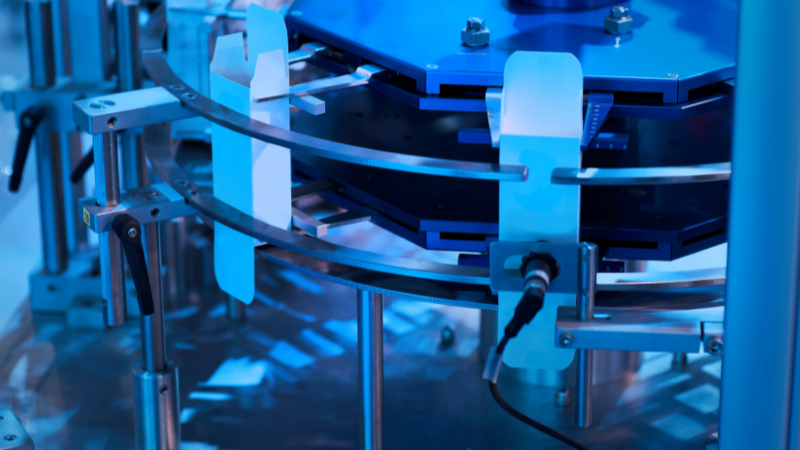
Incorporating die-cutting into manufacturing opens a new world of possibilities, thanks to its adaptability. It finds widespread usage in industries as diverse as they are numerous.
- Packaging Industry: From creating intricately designed boxes to forming protective inserts, die cutting plays a vital role in packaging.
- Automotive Industry: Die-cut components such as gaskets, seals, and insulation parts are commonplace in automotive manufacturing.
- Electronics Industry: Precision-cut parts for electronic devices, including washers, insulators, and shielding components, are made possible with die cutting.
- Medical Industry: Die cutting is crucial in creating precise, sanitary components like medical patches, wound care items, and diagnostic components.
Die-cut parts also frequently appear in the sound and electrical systems of vehicles, and advances in die-cutting technology have also made it possible to build today’s increasingly popular ultra-slim mobile phones. By being instrumental across diverse sectors, die-cutting stands as a universally applicable process with potential benefits for many businesses. However, to grasp its full potential, it’s essential to comprehend the problems this technique helps overcome.
Die-Cutting Machines: Features and Benefits
Before diving into the advantages that come with using die-cutting machines, let’s first familiarize ourselves with their integral aspects.
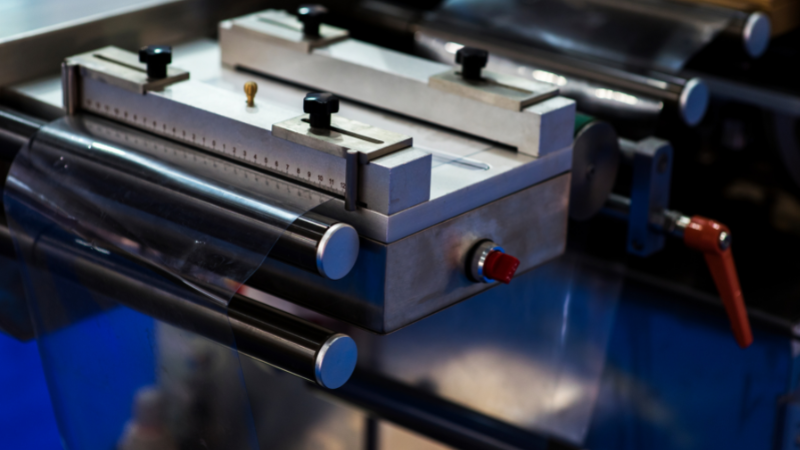
Key Features of Die-Cutting Machines
Die-cutting machines encompass various features that contribute to their effectiveness and versatility in different industrial applications.
- Adaptability: These machines can work with a wide array of materials, including rubber, plastic, fabric, foam, and metal.
- Precision: Thanks to digital or laser-guided technology, these machines can perform extremely precise cuts, even for intricate designs.
- Speed: Die-cutting machines are designed to operate at high speeds, significantly reducing production time.
- Automation: Many machines come with automated features, reducing the need for manual intervention and increasing efficiency.
Benefits of Using Die-Cutting Machines
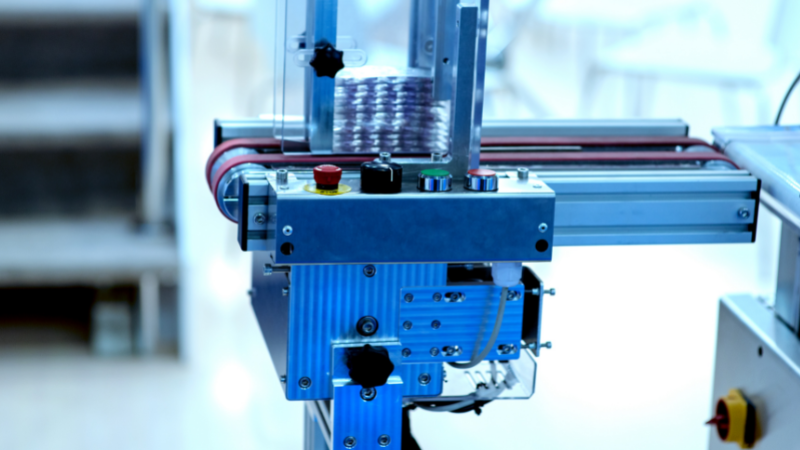
The benefits of using die-cutting machines are abundant and, most importantly, are in direct response to many industry challenges.
- Cost-Efficiency: Die-cutting machines, particularly automated ones, can lead to substantial cost savings in the long run due to decreased labor requirements and reduced waste.
- Versatility: The adaptability of die-cutting machines makes them suitable for different industries and applications, catering to varying needs.
- Consistency: Thanks to their precision and repeatability, these machines can produce consistent, high-quality parts, improving the overall product quality.
- Increased Productivity: The high-speed operation of die-cutting machines boosts productivity, meeting the demands of high-volume production runs.
In essence, die-cutting machines offer numerous advantages that can significantly enhance production capabilities and solve various industry-specific issues.
Manual vs. Digital Die Cutting Machine
To fully appreciate the scope of die-cutting, it’s necessary to compare the two primary types of die-cutting machines: manual and digital. These machines follow different operational principles, each with unique benefits and drawbacks.
Manual Die-Cutting Machines | Digital Die-Cutting Machines | |
---|---|---|
How it works | You feed the material and die manually and turn a handle to cut. | You upload a design to the machine’s software, which then does the cutting. |
What it’s good for | Great for many materials and dies, very versatile. | Best for detailed designs and is mainly used with paper or cardstock. |
Speed and effort | More hands-on work, but can be quick for small jobs. | Can do many things at once and is faster, especially for big tasks. |
Cost | Usually cheaper to buy and run as it doesn’t need power. | More costly, but can save money over time because of its speed and efficiency. |
Ease of use | Easy to use with minimal technical skills. | Takes more time to learn due to the software, but gives you more control over the design. |
Both manual and digital die-cutting machine have their unique strengths and cater to different needs. Your choice will largely depend on your specific requirements, the nature of your projects, and your budget.
Exploring Different Die-Cutting Methods
Die-cutting is a versatile manufacturing process that offers efficient solutions to a wide range of production challenges. By employing different die-cutting methods, manufacturers across many industries can overcome everyday obstacles and streamline their production processes. Let’s delve into the various die-cutting techniques and understand how they solve common manufacturing problems.
Flatbed Die-Cutting: Perfect for Simple Shapes on Flat Materials
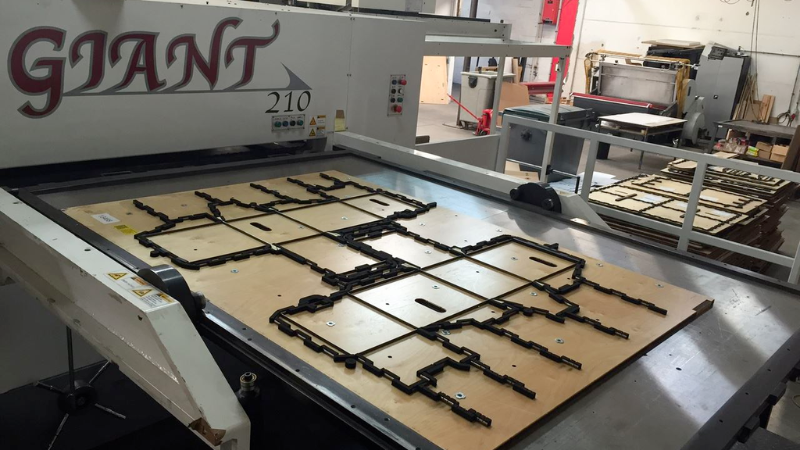
Flatbed die-cutting proves to be the go-to method. This technique involves using a flat surface where the material is placed, while a custom die presses down to cut out the desired shape. Manufacturers often rely on flatbed die-cutting for creating items such as packaging boxes, displays, gaskets, and fabric patterns.
Key points:
- Ideal for simple shapes on flat materials like paper or cardboard.
- Widely used in packaging, display, gasket, and fabric industries.
Rotary Die-Cutting: Uninterrupted High-Volume Production
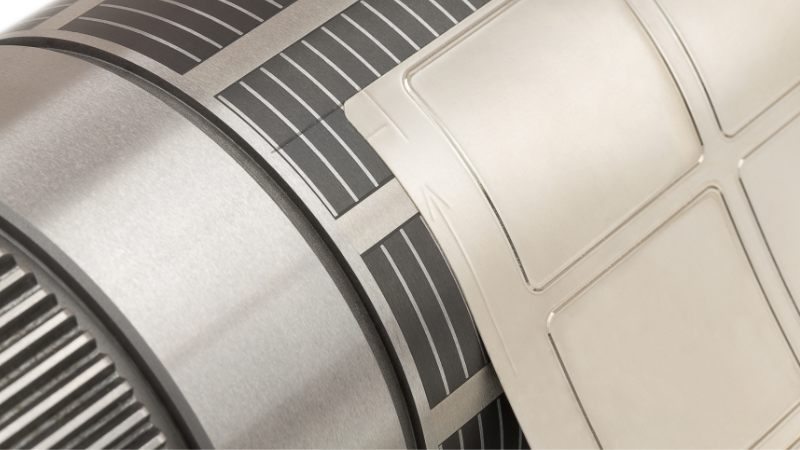
For high-volume production runs that demand continuous cutting without stopping the machine, rotary cutting emerges as an ideal choice. In this method, a cylindrical die with sharp blades rotates against the material at high speeds to achieve precise cuts. The continuous motion allows manufacturers to efficiently produce large quantities of items. Rotary die-cutting machines can cut a multitude of materials for adhesive medical tape, including waterproof adhesive, thermal masking tape, and durable cloth tape.
Key points:
- Enables uninterrupted cutting during high-volume production runs.
- Suitable for producing labels, stickers, plastic parts, and custom-shaped components.
Laser Die-Cutting: Precision Cutting without Physical Contact
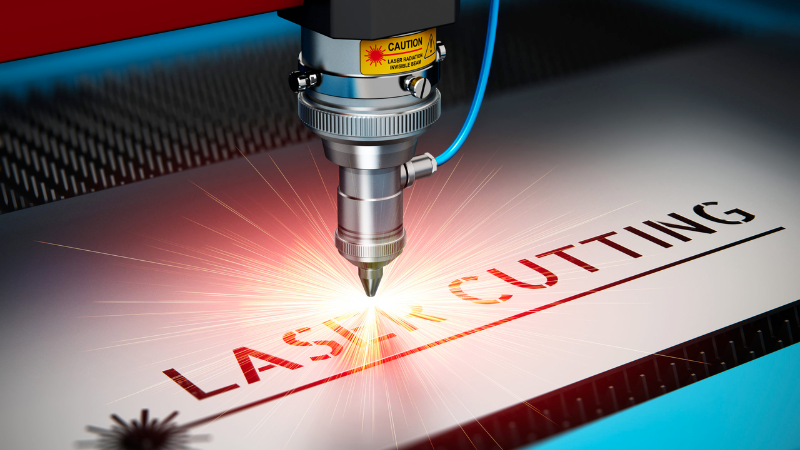
Laser-cutting technology revolutionizes die-cutting by enabling precise cutting of intricate designs on various materials without physical contact. A laser beam replaces traditional blades or punches in this method. It vaporizes or melts away the material along specific paths defined by computer-controlled software. Laser cutting finds applications in industries that require intricate designs, such as electronics, automotive, and medical device manufacturing.
Key points:
- Utilizes laser technology for precise cutting of intricate designs.
- Widely used in electronics, automotive, and medical device manufacturing.
Waterjet Die-Cutting: Gentle Cutting for Sensitive Materials
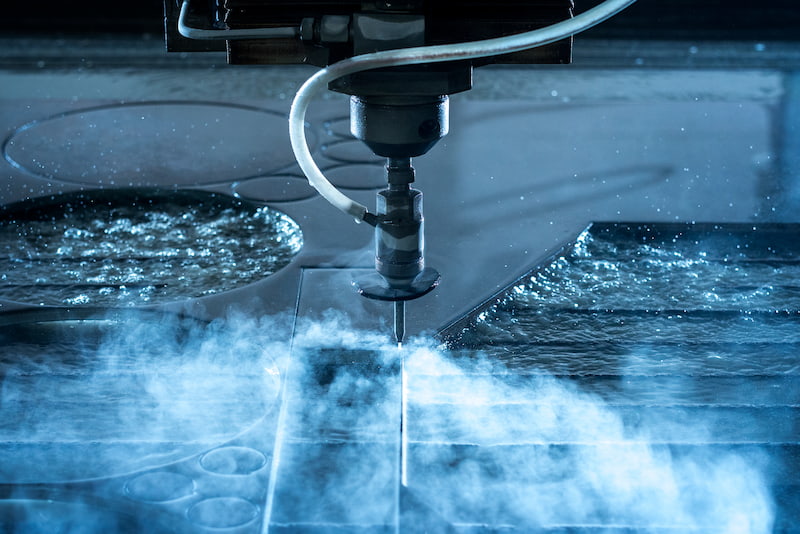
When dealing with materials sensitive to heat or pressure, a waterjet die-cutter offers a gentle alternative. This method employs a high-pressure water stream to cut through the material without causing any damage. Waterjet die-cutting is commonly used in industries like aerospace, textiles, and food processing where delicate materials such as fabrics, composites, and perishable goods need precise yet non-destructive cutting.
Key points:
- Suitable for cutting sensitive materials without heat or pressure.
- Commonly used in aerospace, textile, and food processing industries.
By exploring different die-cutting methods, manufacturers can address specific challenges across various industries. These techniques provide efficient solutions for cutting simple shapes on flat materials or producing intricate designs with precision. Understanding the diverse capabilities of each method empowers manufacturers to optimize their production processes and overcome everyday manufacturing problems effectively.
What is the Best Die-Cutting Method?
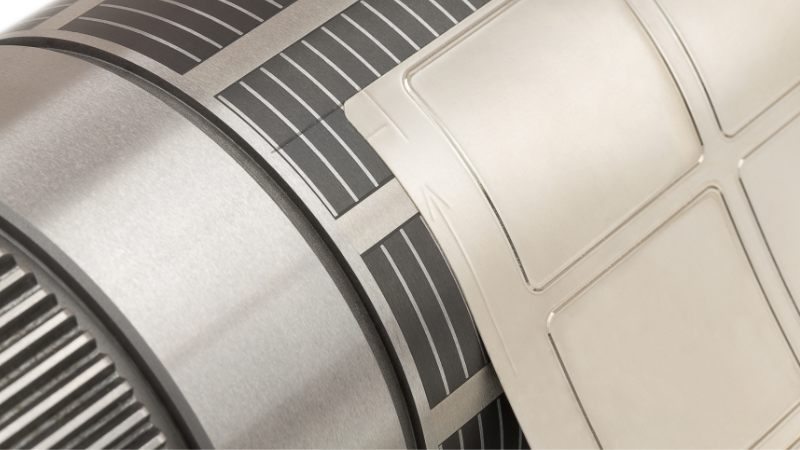
All cutting methods allow you to create several products and components. In addition, they have high accuracy, volume production, and quality. Nevertheless, all die-cutting techniques do not have the same capabilities. Consequently, we discuss the most straightforward and fastest way.
The Simplest Die-Cutting Process
Flatbed cutting is the simplest method for general cutting, suitable for low-volume production. This versatile method allows you to cut and shape different types of material. Furthermore, the process is ideal for cutting adhesive sheets. Generally, changeovers in flatbed cutting are quick, easy, and fast. Also, the cost of dies is cheaper compared to other die-cutting methods.
The Fastest Die-Cutting Process
Rotary die-cutting is the fastest die-cutting method, making it cost-effective. The process uses rotating cylinders to cut heavy rolls of raw material. Then, Because the material is fed rapidly into the machine, the flexible die quickly cut large quantities of die into high-quality products.
How Die-Cutting Solves Everyday Manufacturing Problems
Die cutting has proven to be an extremely versatile manufacturing process, capable of addressing a multitude of challenges faced by industries today. Here are some examples:
High-Volume Production
Die cutting excels in high-volume production scenarios where consistency and speed are crucial. The automated nature of the process enables swift, precise cuts for thousands of units, significantly enhancing productivity.
Complex Shapes
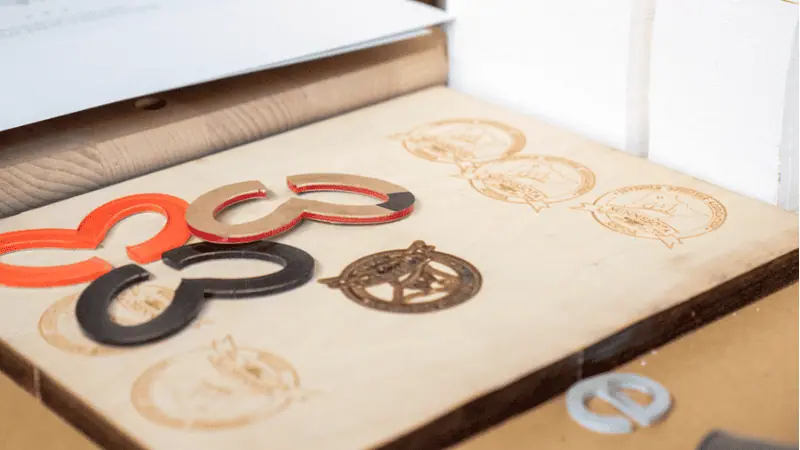
Manufacturing parts with complex or intricate shapes can be challenging. With die cutting, particularly laser die cutting, these shapes can be accurately reproduced with high precision.
Material Wastage
Die cutting is designed to maximize material usage, reducing waste. By carefully planning the layout of the cuts on the material, it is possible to get the most parts out of a single sheet, promoting sustainability and cost-efficiency.
Time Constraints
The speed and efficiency of die-cutting make it an ideal solution for projects with tight deadlines. By accelerating the production process, manufacturers can meet their time constraints without compromising on quality.
By addressing these and other challenges, die-cutting offers immense value across numerous industries, from packaging and printing to electronics and automotive manufacturing.
Addressing Common Problems in the Printing Process with Die-Cutting Solutions

The printing industry is not exempt from operational challenges. From ensuring uniformity in product sizes to maintaining high production volumes without compromising quality, various hurdles might arise. Thankfully, die-cutting offers solutions to many of these common problems, enabling more streamlined and efficient printing processes.
Ensuring Consistent Product Sizes and Shapes
In the printing industry, consistent product sizes and shapes are crucial, whether for printed labels, business cards, or packaging materials. Variances in size or shape can lead to product waste, increased costs, and potential customer dissatisfaction. Die-cutting provides an answer to this issue, offering precision cuts that ensure consistent product dimensions every time.
High-Volume Production
Printing businesses often deal with high-volume orders that require fast turnaround times. Die-cutting machines, especially those with automation capabilities, can significantly speed up the production process. These machines can quickly produce a large quantity of printed materials, helping businesses meet their delivery schedules.
Enhanced Product Quality
The quality of printed materials directly impacts a company’s image and customer satisfaction levels. Die-cutting machines deliver high-quality cuts, leading to products with clean edges and a professional appearance. Furthermore, the precise cuts of die-cutting machines reduce the risk of tearing or damaging the printed material, further enhancing product quality.
Minimizing Waste
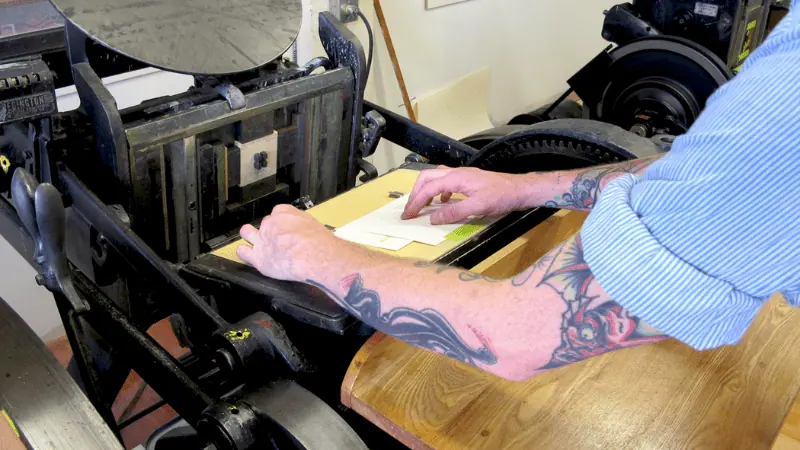
Inefficient cutting processes can result in excessive material waste, increasing production costs. The precision of die-cutting minimizes material waste, as the cuts are designed to utilize as much of the material as possible. This efficient use of materials not only reduces costs but also contributes to sustainable business practices.
Customization Capabilities
In today’s competitive market, the ability to provide customized solutions is a significant advantage. Die-cutting machines can accommodate a wide variety of designs, enabling businesses to offer customized printed products to meet their client’s unique needs.
In conclusion, die-cutting is an effective solution to several common problems in the printing industry. By offering consistent, high-quality products at high volumes, with minimized waste and customization capabilities, die-cutting is an invaluable tool for modern printing businesses.
How to Choose the Correct Type of Die Cutter for Your Needs?
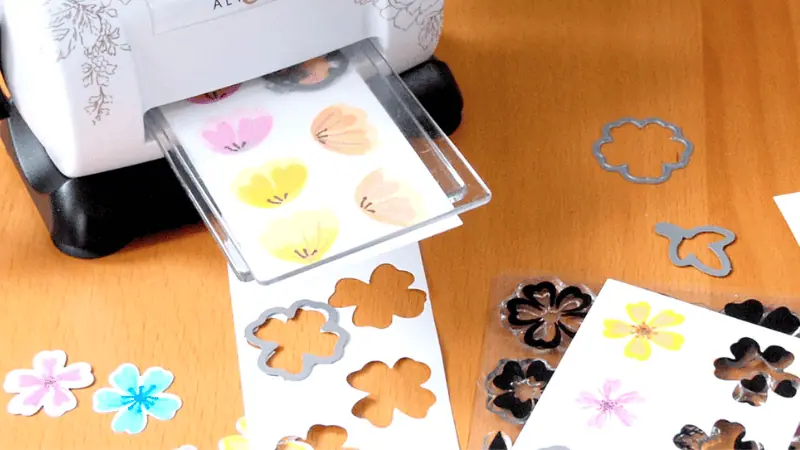
There are several important factors to consider. By evaluating these factors and assessing the available options, you can ensure that you choose the correct type of die cutter that aligns with your specific requirements.
Consider Material Type, Design Complexity, and Production Volume
The first step in choosing the right die cutter is considering the material type, design complexity, and production volume requirements. Different types of die cutters excel in handling various materials and design intricacies. For example:
- Flatbed Die Cutters: Ideal for cutting thin materials such as paper and cardstock.
- Rotary Die Cutters: Well-suited for thicker materials like corrugated cardboard or foam.
- Digital Die Cutters: Perfect for intricate designs and small production runs.
By understanding the characteristics of your materials and desired designs, you can narrow down your options to find a die-cutter that meets your specific needs.
Evaluate Features and Capabilities
Once you have identified potential die cutters based on material type and design complexity, it’s crucial to evaluate their features and capabilities. Each machine may offer different functionalities that can enhance productivity or improve efficiency. Some key features to consider include:
- Cutting Speed: Determine if the machine can meet your production volume requirements within a reasonable timeframe.
- Automation Options: Assess whether automated feeding or stacking systems are available to streamline operations.
- Tooling Flexibility: Look for machines that allow easy tool changes or customization to accommodate future design variations.
By carefully examining these features, you can select a die cutter that not only meets your current needs but also provides room for growth and adaptability in the future.
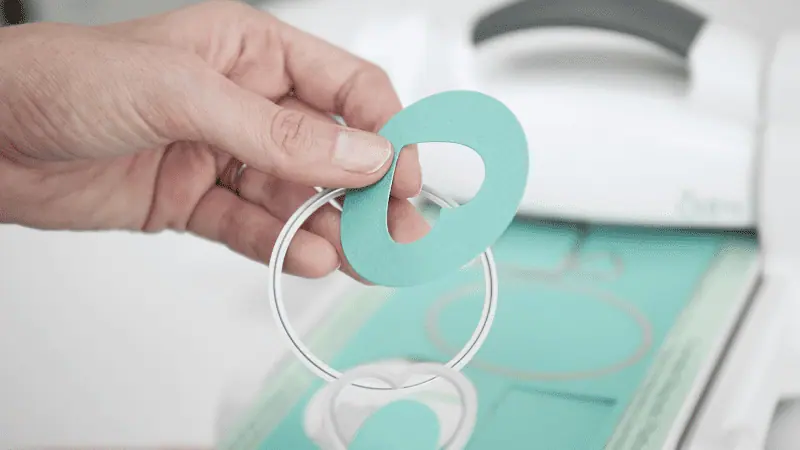
Assess Long-Term Costs and Maintenance Requirements
In addition to upfront considerations, it’s essential to assess the long-term costs associated with each type of die cutter. This includes evaluating maintenance requirements, consumable expenses, and the availability of spare parts. Some machines may require more frequent maintenance or have higher operating costs due to specialized tooling or proprietary components.
To make an informed decision, compare the total cost of ownership over the expected lifespan of the machine. Consider factors such as:
- Maintenance Contracts: Determine if service agreements or warranties are available to minimize unexpected repair costs.
- Consumables: Evaluate the ongoing expenses for blades, cutting mats, or other consumable items required for operation.
- Spare Parts Availability: Research the availability and lead times for replacement parts to avoid prolonged downtime.
By considering these long-term costs and maintenance requirements upfront, you can ensure that your chosen die-cutter remains a cost-effective solution in the long run.
Seek Expert Advice
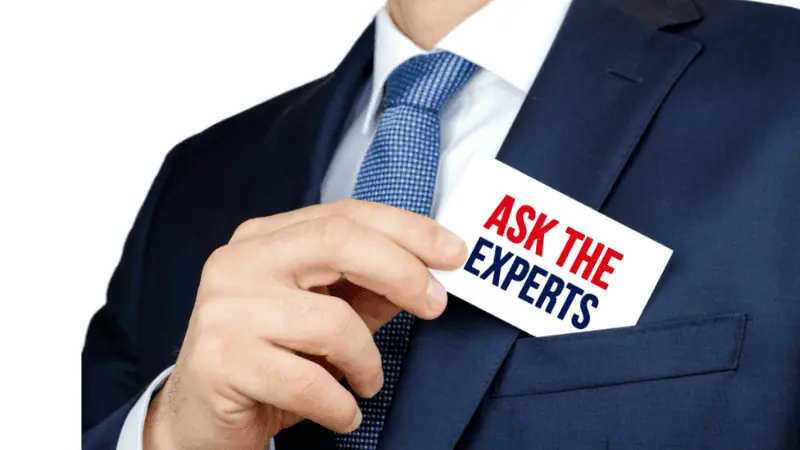
Choosing the correct type of die cutter can be a complex decision with various variables to consider. To make an informed choice, it is advisable to seek expert advice from industry professionals or consult directly with manufacturers. They can provide valuable insights based on their experience and knowledge of different die-cutting solutions.
Engaging in conversations with experts allows you to ask specific questions tailored to your manufacturing needs. They can guide you through the selection process by recommending suitable types of die-cutters based on your unique requirements.
Conclusion
In summary, die-cutting is an incredibly versatile and valuable tool in the manufacturing industry. By understanding the die-cutting process and its various methods, businesses can make informed decisions that best fit their needs.
Ultimately, whether manual or digital, flatbed or rotary, the right die-cutting approach can optimize manufacturing processes, enhance product quality, and lead your business toward greater success.
Why go to Hongju for your Die-cutting Manufacturing needs?
Selecting Hongju Silicone for your die-cutting manufacturing needs is choosing excellence and reliability. With years of industry experience, cutting-edge technology, and a reputation for high-quality work, we deliver precise, efficient, and cost-effective die-cutting solutions tailored to your specific needs.
Take the First Step:
Requst for an Inquire
Quality Meets Affordability. Inquire Now for High-Quality Products at Low Volumes.