The O-ring groove is not a one-size-fits-all. When designing the track, it is essential to specify certain parameters specific to the O-ring for the best results.
This article delves into the intricacies of O-ring groove design with CAD software and its practical application in your projects.
Stay with us as we unfold the essential steps and tips to effectively incorporate O-ring grooves into your work, enhancing efficiency and precision!
What is an O-ring Groove/Gland Shape?
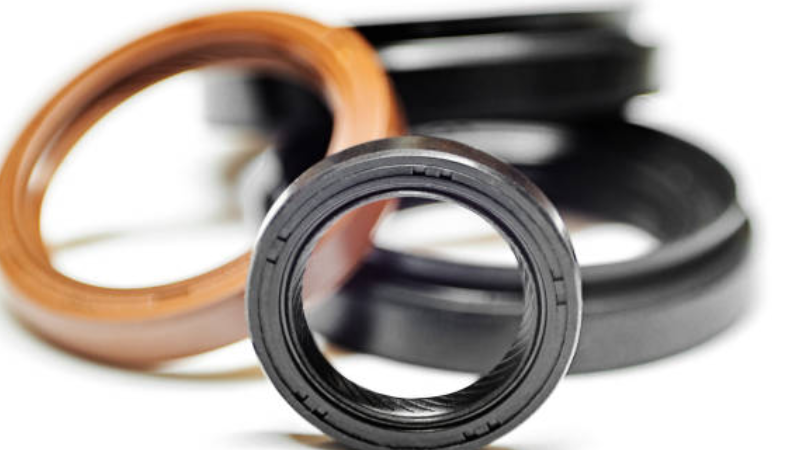
An O-ring groove/gland shape supports the seal and provides the necessary deformation for proper functionality. Therefore, the body is one of the most important considerations when designing an O-ring groove. The correct O-ring groove dimensions and shape will ensure complete compression between the track and the mating surfaces.
Furthermore, the O-ring groove has triangular, rectangular, or dovetail shapes. Before choosing a profile, you have to consider the O-ring application. In addition, always choose a figure that is easy to machine without sharp edges. A groove shape with sharp edges may cause a deterioration in the O-ring seal.
Therefore, every sharp corner should have a groove radius. Also, the interfacing corners should be rounded to reduce damage to the O-ring during installation. A typical O-ring groove shape is rectangular with rounded edges. This shape provides uniform compression for the sides of the O-ring, interfacing with the gland.
How to Create an O-ring Groove in Your CAD Software
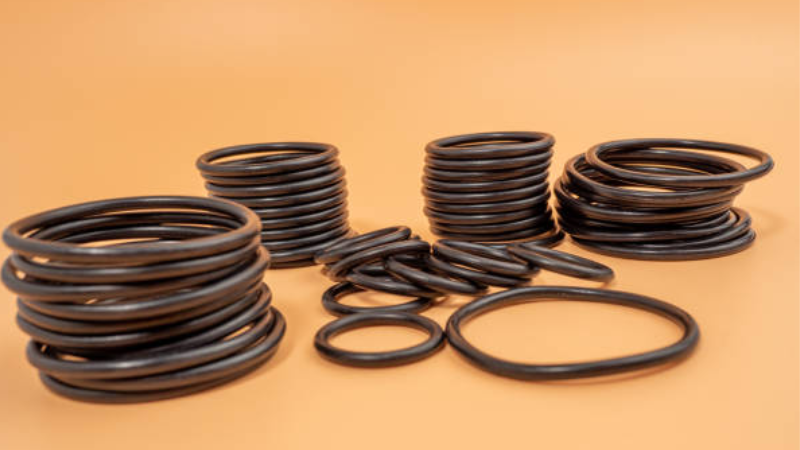
Computer-aided design (CAD) software is a program that lets you design and visualize the construction of an O-ring groove. Consequently, you can create more accurate designs, make alterations, and optimize your O-ring track before production.
When using this software for your O-ring groove, you must specify parameters to create more detailed designs. These parameters include:
1. O-Ring Groove Width
The O-ring groove width is the groove’s horizontal span. Its width should allow the O-ring to expand fully within the groove when designing the track.
However, the groove width should allow O-ring diameter expansion to a maximum of 5%. Furthermore, the gland’s outside diameter (OD) should be greater than the O-ring’s inside diameter (ID) to allow for stretching when installed.
Suppose the O-ring won’t be installed in a gland. In that case, the design of the O-ring interface should not require more than a 100% stretch during the O-ring’s installation.
As mentioned earlier, the O-ring stretch should ideally be 5% when installed in a gland. Specifying the gland ID during the design can help minimize installation stretch. It is essential to minimize installation stretch to prevent pressure buildup in the material.
This also helps to reduce the compression percentage in the O-ring and the cross-sectional area.
You can calculate the O-ring groove width using this formula;

2. O-Ring Groove/Gland Volume
Specifying the correct groove volume for the O-ring to fill is also essential. Groove volume allows for the O-ring’s thermal expansion and increasing width due to squeezing.
In addition, the groove volume is also necessary because the O-ring may swell when it soaks up fluids. For space, the optimal gland volume should be 15-25%. When the room is filled with the O-ring material, the gland volume should be between 75-85%.
For guidance on specific groove types and interfaces, it is essential to check industry specifications and other resources for O-ring design
You can calculate the gland fill percentage using this formula:
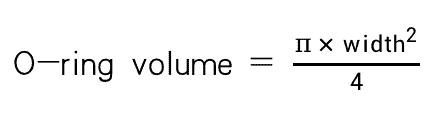
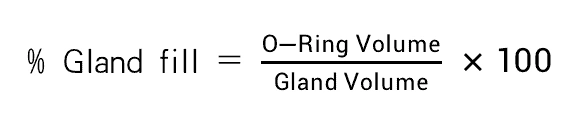
3. O-Ring Groove/Gland Depth
O-ring groove depth depends on the width and the maximum compression allowed for your application. Therefore, it is essential to maintain a specific compression ratio for complete sealing and not compromise the elastomer’s integrity.
You can calculate the compression ratio using this formula:

Take the First Step:
Requst for an Inquire
Quality Meets Affordability. Inquire Now for High-Quality Products at Low Volumes.
The Different Types of O-ring Grooves You Can Use in Your Designs
There are different types of O-ring groove designs, and they depend on the application. The types of O-ring grooves include:
Industrial Static/Radial Seals
Static applications involve parts that are not moving. O-rings used in this application seal two mating components that are not in motion. When designing grooves for this application, consider the direction of the pressure.
If the application involves outward pressure, the track OD is primary. In addition, the groove width should be considered for the ID.
For inward pressure, the ID is primary. This parameter ensures that the O-ring moves the least distance to seal the gap.
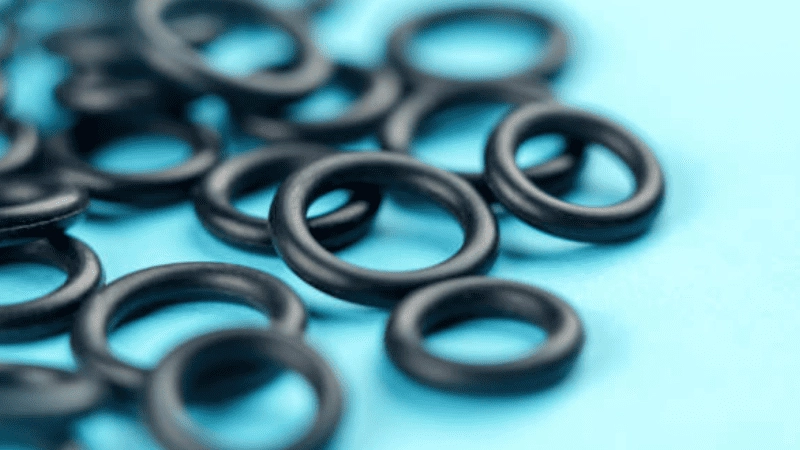
Industrial reciprocating/Dynamic Seals
Dynamic applications require seals that create a barrier between surfaces in linear, rotary, or oscillatory motion. Reciprocating applications use hydraulic or pneumatic seals.
Dynamic applications with short strokes need O-ring grooves with small diameters. More extended stroke applications will perform well with thick cross-sectional O-rings. In dynamic applications, the seals do not need as much compression as static seals.
Face seals / Flange
The face seal is used for applications where the sealing surface and the seal’s axis are normal. This seal prevents leakage in the radial direction of the seal’s axis. Furthermore, the flange or face seal does not have a gap between surfaces, and they eliminates extrusion design issues.
Static vs. Dynamic O-Ring Groove Design Considerations
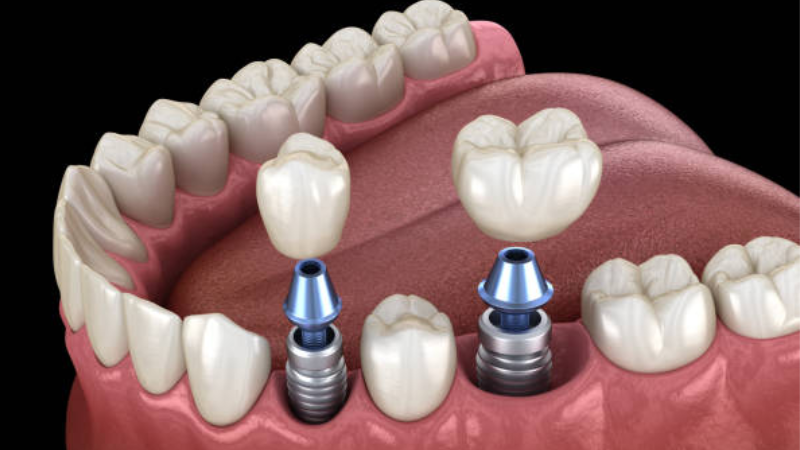
Static and dynamic applications are different. Hence, they need different types of O-rings. For instance, static applications are stationary, and the O-ring seals two components that don’t move at all.
Therefore, swelling is more likely to occur with the O-ring in a static application. Static O-rings are elastomers, including axial, crush, dovetail, and radial seals.
On the other hand, dynamic applications have two parts moving concerning each other. In this type of application, material deterioration is more likely. The best seal types for this process are rotary, reciprocating, or oscillating seals.
Take the First Step:
Requst for an Inquire
Quality Meets Affordability. Inquire Now for High-Quality Products at Low Volumes.
Tips for Using O-ring Grooves in Your Projects
- Avoid overstretching
O-rings have their maximum stretch point, and overstretching them can lead to a break or tear during use. Also, when fitting the O-ring in the groove, ensure that the stretch is even and does not exceed the maximum elongation.
- Use the correct O-ring size.
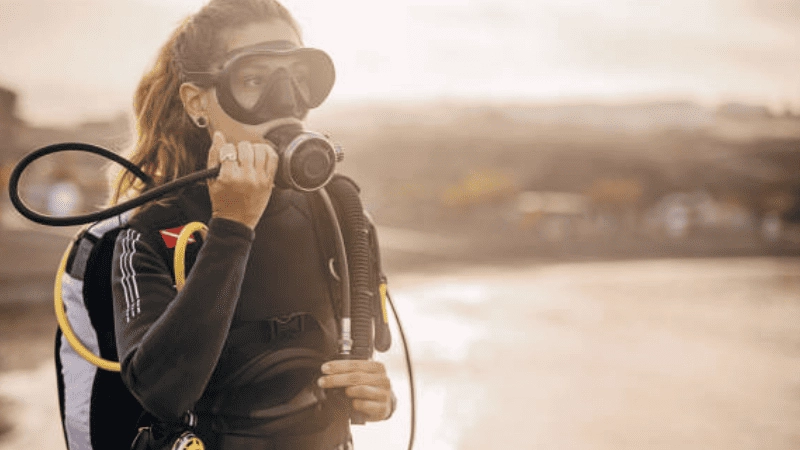
All projects are unique. It is, therefore, best to get an O-ring that fits the groove of your application. Too large O-rings do not provide adequate sealing, and too small O-rings will tear or break.
- Avoid sharp edges
O-ring grooves sometimes have sharp corners or edges. These sharp edges can tear the O-ring, resulting in leaks. Instead, you can lubricate the O-ring before fitting it in a groove.
- Slide, don’t roll
Rolling O-rings while fitting them in a groove only results in a spiral. This spiral limits the functionality of the O-ring, resulting in leaks and damage. Instead, slide the O-ring into the groove. You can also use a lubricant to help the O-ring slide in more easily.
Examples of How to Use O-ring Grooves in Real-World Applications
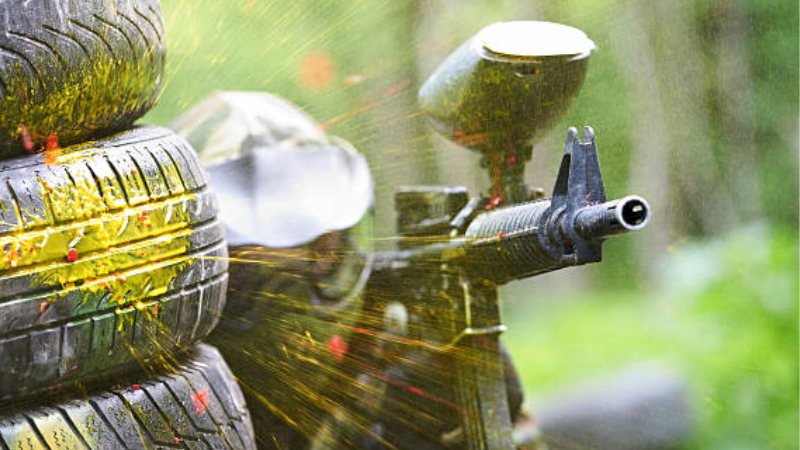
O-rings are used in mechanical processes that especially involve extreme temperature and high pressure. O-ring grooves are helpful in many applications, including boilers, engines, and compressors. However, you can find O-ring tracks around you. Real-world applications of O-rings include;
- Scuba gear: the breathing apparatus is an essential component of scuba gear. An O-ring keeps water out and air in for the breathing apparatus. Before diving, divers usually check the seal on their air tank to ensure it is functioning properly.
- Paintballing: a paintball game is fun, allowing you to shoot paint at your unsuspecting enemies. O-rings keep the air sealed in the paintball gun, helping you deliver powerful shots.
- Dental implants: dental implants protect your teeth. However, liquid entering the implant can cause excruciating pain or infection. Medical-grade silicone O-rings are used to seal implants and keep the fluid out.
Take the First Step:
Requst for an Inquire
Quality Meets Affordability. Inquire Now for High-Quality Products at Low Volumes.
Conclusion
O-rings are generally excellent seals for keeping fluids out and protecting a component. However, an O-ring has to fit in a groove for maximum sealing. Sometimes the track may not match the O-ring, leading to damage and leaks.
And that is why it is essential to design an O-ring groove. You can use CAD software to create your O-ring using parameters like groove width, volume, and depth.
Contact Hongju For Your O-ring Needs!
With over 20 years of expertise in rubber manufacturing, Hongju delivers precision O-rings tailored to your exact requirements.
From design to prototyping, we ensure flawless performance and reliable sealing for your applications. Collaborate with us today to accelerate your project and stay ahead of the competition.